Importance of Grinding Mills in Mineral Refining
The main function of grinding mills is to minimize the size of the rock particles to a size that can be further reused. The process of grinding includes the use of a grinding medium, which is often a ball or a rod. The grinding medium is rotated inside the mill, leading the rock particles to be crushed and ground to a fine powder.
Grinding mills are essential in mineral processing procedures because they are responsible for crushing and grinding the rocks into fine particles. The size of the particles is important since it decides the capability of the further processing steps. If the particles are too large, they may not be fully refined, but if they are too small, the capability of the process may be decreased.
The efficiency of grinding mills is also important in terms of consuming the energy. Grinding mills takes a large amount of energy during the procedures, and enhancing their operation Is important to decrease energy consumption and costs.
Here is how a rock-solid mineral is crushed finely into powder by our Grinding mills.
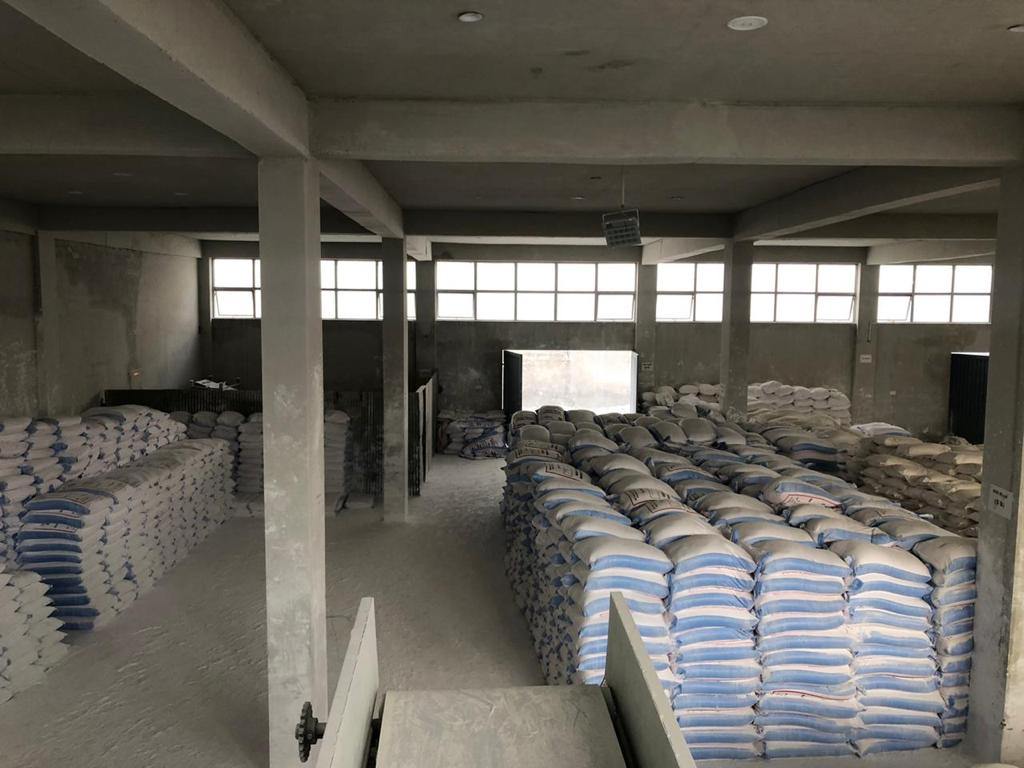
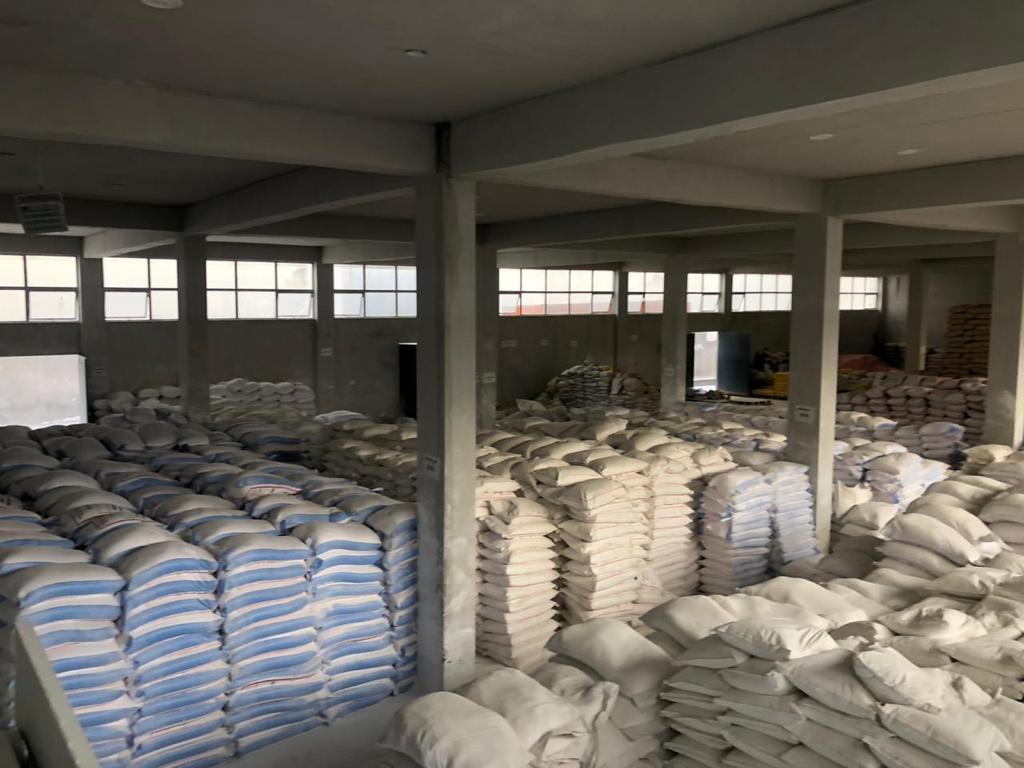
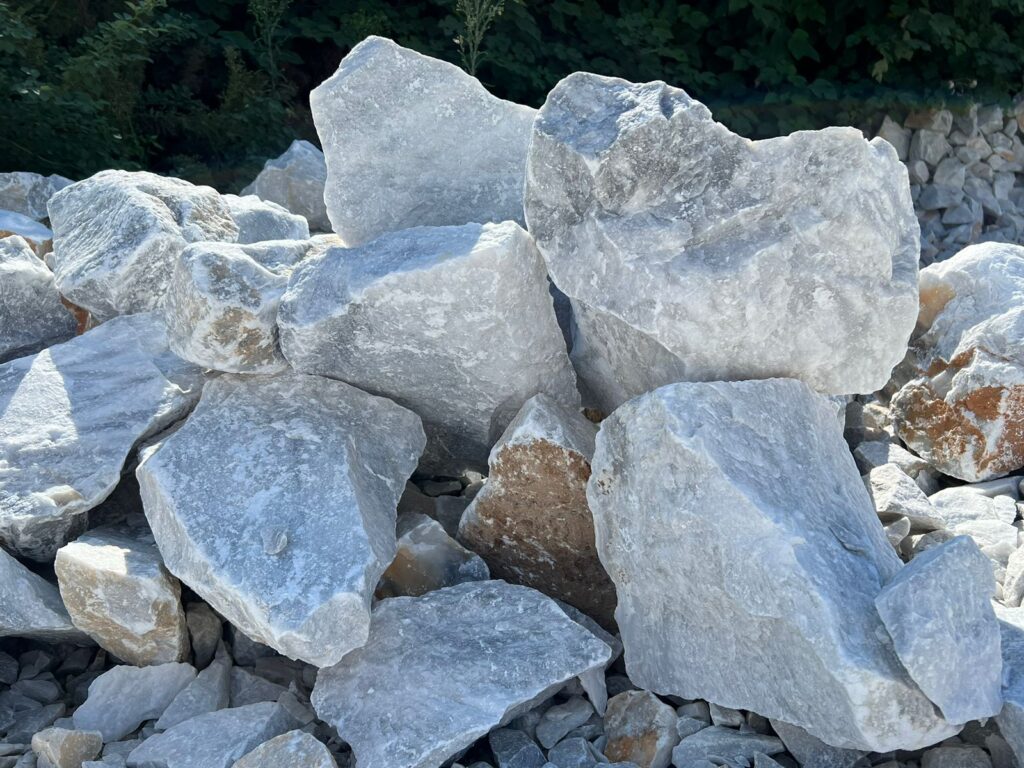
Kinds of Grinding Mills
There are different types of grinding mills that are mainly used in mineral processing Procedures. Each kind of grinding mill has its special characteristics and benefits, and the decision of the proper type of mill rely on the technical requirements of the procedure.
BALL MILLS
Ball mills are the most frequently used mills in mineral processing operations. They are made of a rotating cylindrical shell, which is partially filled with grinding media, such as balls or rods. The material to be ground is fed into the mill through a hollow turn-on at one end of the shell. The grinding media inside the mill crushes and grinds the material, producing a fine powder.
Ball mills are highly efficient and can produce fine particles quickly. They are also versatile and can be used for both wet and dry grinding. However, they consume a significant amount of energy and may produce a lot of heat during operation, which can affect the quality of the final product.
ROD MILLS
Rod mills are similar to ball mills, but instead of using grinding media, they use rods to grind the material. The rods are placed inside the mill, and as they rotate, they crush and grind the material, producing a fine powder.
Rod mills are generally more efficient than ball mills and can produce fine particles quickly. They are also more suitable for grinding harder materials, such as ores and minerals. However, they are less versatile than ball mills and can only be used for dry grinding.
AUTOGENOUS MILLS
Autogenous mills are grinding mills that use the ore itself as the grinding medium. The ore is fed into the mill, and as it rotates, it crushes and grinds itself, producing a fine powder.
Autogenous mills are highly efficient and can produce fine particles quickly. They are also versatile and can be used for both wet and dry grinding. However, they are less common than ball mills and may require more maintenance.
SEMI-AUTOGENOUS MILLS
Semi-autogenous mills are similar to autogenous mills, but they use a mixture of ore and grinding media to grind the material. The grinding media is usually steel balls, and the ore is fed into the mill through a hollow trunnion at one end of the shell.
Semi-autogenous mills are highly efficient and can produce fine particles quickly. They are also versatile and can be used for both wet and dry grinding. However, they are less common than ball mills and may require more maintenance.
Conclusion
Grinding mills play a crucial role in mineral processing operations, as they are responsible for crushing and grinding the ores into fine particles that can be further processed. The selection of the appropriate type of mill depends on the specific requirements of the operation, and each type of mill has its unique features and advantages.
Ball mills, rod mills, autogenous mills, and semi-autogenous mills are the most commonly used mills in mineral processing operations. Each type of mill has its unique advantages and disadvantages, and the selection of the appropriate type of mill depends on several factors, including the specific requirements of the operation, the type of material being processed, and the desired particle size of the final product